Do It Yourself Vacuum Forming For The Hobbyist Pdf Converter
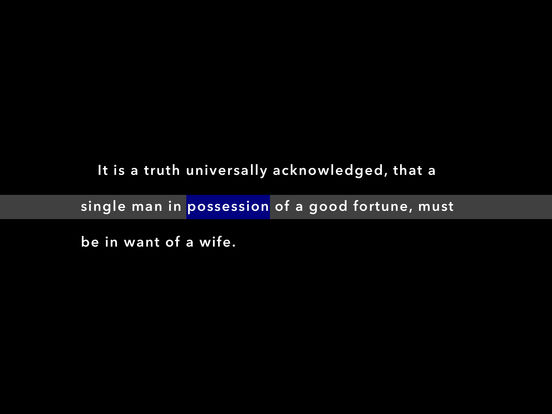
[This blog post is adapted from a couple of postings in the 'making the plastic clamping frames' thread over at TK560.com.] In the kitchen vacuum forming Instructable I describe how to make aluminum plastic clamping frames from window screen frame material. Those frames are nice because they're easy to make, and you can mix and match side lengths to get various sizes and aspect ratios for different projects. Aluminum window screen frame material is a bit flimsy, however, so if you're making big stuff or using really thick plastic, you may want something more rigid.
Vacuum Forming for the Hobbyist PDF eBook digital download 12.95. Learn how to use heat and vacuum to mold flat plastic sheets into complex shapes. Plans for building a table top Hobby-Vac vacuum forming machine. Hobby Vacuum Former - Make Your Own Thermoform Plastic Prototypes, Clamshell Packaging, Custom Molds, Scale Model Parts, and Movie Props - WidgetWorks. 31-DP-00935 - Carousel Clamp Rack Downloadable Woodworking Plan PDF.
Aluminum C-channel is a good choice, too. You can find it in several sizes and a couple of thicknesses at a home improvement store like Home Depot or Lowe's. This is a small (12 x 18') frame made of small C-channel (3/8', 1/16' or 1/20' thick), but the same technique works for larger frames made of correspondingly larger and thicker C-channel.
The basic technique is just to cut slits in the horizontal parts of the C profile with a hacksaw, and bend the vertical part to make the corners. (Be careful not to score the vertical part while sawing through the horizontals, or it may tear there.) Where the C-channel comes back and meets itself, there's a little extra piece with the horizontals cut off, to make a tab.
The tab is also bent at 90 degrees, to overlap the vertical at the other end. Both are drilled, and pop-riveted together. (Or you could use a small bolt.) For thicker material than I used here, such as 1/8' aluminum, it's also a good idea to drill 1/4' holes through the horizontals right next to the vertical part, and saw the slit until it meets that hole. (That takes away horizontal material near the bend point, so that it can bend over a slighly larger radius, and not fracture.) Rigidity of a solid is generally proportional to the cube of the thickness, so one frame twice as thick is 8 times as rigid.
(Or 4 times as rigid as two frames.) 3/8' thick C-channel is considerably more rigid than window screen frame stuff, and 3/4' C-channel is way, way more rigid. You only need one frame that's pretty rigid. The other one only needs to be rigid enough to spread a fair bit of the clamping force halfway from one clamp to the next. To maximize rigidity for a given cost, you should generally combine one thick, rigid frame with a thinner, more flexible one.
(Even if the cost of the frame material is no object, that's usually a good idea, at least for metal frames. Metal frames act as heat sinks and make it harder to heat the edges of the plastic, or take longer to preheat the frames. Minimizing the amount of metal needed to get the necessary rigidity is usually a good idea.) So, for example, you might make one frame out of 3/4' C-channel 1/8' thick, for overall rigidity, and another out of 1/4' C-channel 1/16' thick. Del Taco Drivers Usb 2. That will be stiffer than a pair of frames made out of 1/2' C-channel.
Making the top and bottom frames different also gives you some interesting choices. You can have one frame that's rigid along the sides, and another that's fairly flexible along the sides but has rigid corners. Once you clamp them together, they'll be fairly rigid all around. One version of that would be to make a main frame out of 3/4' or 1' C-channel, with the horizontal parts cut to let you bend the vertical parts.
That gives you rigid bars but not very rigid corners. You can combine that with a matching frame made out of aluminum windowscreen stuff, which is flimsy (and inexpensive) but has rigid right-angle corners.
Between the two of them, you get rigid bars and fairly rigid corners, with no welding or brazing. (There's a gotcha here, though, if you're using a platen with a gasket; I'll explain that below. The frames shown were made for a platen whose edge seals directly to the hot plastic, so that the rubbery plastic acts as its own gasket. If you don't know what that means, and you're curious, check out the 'Platen Design and Construction' link in the sidebar.) Here's an example of that, with a small frame made of 3/8' C-Channel paired with a window screen-type frame, clamped around a piece of plastic: The same scheme would work with a much larger frame made of, say, 3/4' C-channel made of 1/8' aluminum. The other frame could still be made of window screen frame stuff; as long as you have clamps every few inches, it's rigid enough to hold the plastic against the more rigid frame. Here's a shot where you can see the tab riveted in place to close the rectangle: I epoxied the joint (and the hole through the rivet) with J. Weld to make it air tight there in case I used that frame with a gasket system.
(It was built for an direct edge-sealing platen with no gasket.) The gotcha with mixing C-channel frames and window screen frames is that the positioning of the clamps (binder clips) can interfere with the gasket seal. With two C-channel frames, the clamps can go inside the C's of both frames, and the bottom of the bottom frame is left flat to seal against the gasket. With two windowscreen frames, you can just put the binder clip around both frames, with the rolled edge extending inward past the frames to clear the gasket and leave the bottom flat where it meets the gasket. But with one frame of each type, you can't really do either---if one edge your clip goes inside the C channel, that stops it from moving inward further than the frame, and the rolled edge on the other side is stuck against the window screen frame where it meets the gasket.
So if you mix the two, the C-channel frame has to go on bottom, because the binder clip can go inside it and not mess up the seal. That may not be what you want, if you're using C-channel to make a thick, rigid frame. (Generally you'd like the thinner frame on bottom, so that it doesn't raise the edges of the plastic way above the platen.) In that case, you may be better off with two C-channel frames, with big C-channel for the top frame, and small for the bottom one. To get good corner rigidity using only C-channel, you can attach flat L-shaped angle braces to the top horizontal parts of the top frame. (That's one advantage of C-channel over L-profile aluminum---the upper surface of the top frame can have something riveted or bolted to it without interfering with the surface that meets the plastic.) A couple of L-braces on diagonally opposed corners makes the frame almost as rigid as braces on all four corners. Some tips on cutting, bending, and drilling the aluminum: 1.
Use a hacksaw, and a miter box if you have one, to get the two slits aligned at each bend. Disaligned slits may make it prone to bending out of a plane and making a warped frame. Blue Diamond Usb To Serial Driver. Be careful not to score the vertical part when you cut the horizontal parts.
For thicker material than I used here, such as 1/8' aluminum, it's also a good idea to drill 1/4' holes through the horizontals right next to the vertical part, and saw the slit until it meets that hole. (That takes away horizontal material near the bend point, so that it can bend over a slighly larger radius, and not fracture. It also makes it easier to cut through the horizontals without going so far as to score the vertical. I got this tip from Doug Walsh's excellent book, Do it Yourself Vacuum Forming for the Hobbyist, where he applies it to similar frames made of L-profile aluminum.) 3. For drilling, start by making a pilot dent with a punch or a hammer and a nail, then drill a small pilot hole, then the 1/4' hole.
Don't try to drill a 1/4' hole without a pilot hole. While drilling metal, use a slow speed and go slow. Spinning the bit too fast just generates extra heat from friction. Frequently pull the bit up and blow the chips out. (Aluminum is not very hard to drill, but this is good advice anyway.) 5.
When bending the corners, do it against something flat, and sweep one side slowly through 90 degrees. (I did it against my glass patio door.) EDIT 10 Sept. It seems that C-channel frames are also in Doug's book.
Yet another Walsh wheel I've reinvented. I've also come across a commercial vacuum former using this kind of frame, with L-shaped braces riveted to cut-and-bent C-channel to make the corners rigid. You can make a good vacuum former for about $40, in an hour or so, and use your kitchen oven to heat the plastic, and your vacuum cleaner to suck the hot plastic into shape.
Check out at www.Instructables.com for detailed instructions on how to make one. (It doesn't require any special tools or skills.) Here's a little demo movie of the cheap homemade vacuum former in action: As you can see in the video, this high-tech 'vacuum forming machine' is mostly a board with a hole in it and a gasket (made of weatherstripping foam tape from the hardware store), plus a pair of homemade aluminum frames to clamp the plastic between (made from DIY windowscreen frame parts that you just cut to size and plug together). What's not obvious from the video is that this isn't just a cheap vacuum former---it's actually a good one. It's more capable than most homemade vacuum formers that you may have seen---those boxes covered with pegboard---and better than machines you can buy for $250. You can easily upgrade it to add an inexpensive high-vacuum system for forming thick plastic and/or getting finer detail, or add a standalone oven for about $30 so that you're not stuck in the kitchen. (See the sidebar for a link on how to make your own oven.).
I wrote an Instructable on converting an old-school 'floor pump' (bike pump) to a manual vacuum pump, for a total cost of about $18. (You could actually do it for around $13 with a little more effort.) The Instructable got picked up as the Hack of the Day on www.hackaday.com a few days later, and got several thousand extra views because of it. Here's a little video of using the vacuum pump on peeps in a mason jar: A manual vacuum pump can be used with a small vacuum former for the occasional item formed from thick plastic. You wouldn't want to do it a bunch of times a day, though, unless you want to build up your biceps. It can also be useful for vacuum pressing wood laminates or vacuum bagging composites.
(A similar but smaller pump is used for vacuum bagging small things like skateboards.). The best places to look for information (and help) about do-it-yourself vacuum forming and homebuilt vacuum formers are: 1) The Vacuum Forming forum on. TK560 is the most active site on the web for information and advice on making and using your own vacuum former. Is largely oriented toward Star Wars fans who make their own costume armor (stormtroopers, etc.) but the vacuum forming forum is general. It's also very friendly and helpful.
Various people there make aftermarket automotive parts, replacement car and airplane parts, model parts (plane parts, boat hulls, and car bodies), and custom furniture, as well as costume stuff (masks, armor, props, etc.). A number of people there have built largish vacuum formers more or less according to plans in Thurston James's book,. (The book is not free, but it's a good deal.) The standard size 'TJ machine' is 2 feet by 2 feet (or 4' x 4'!), but there are 2' x 3', 2' x 4', and metric variants. You can build a 2 x 2 foot former with its own oven for under $200, if you're content with a vacuum cleaner as a vacuum source. (That's fine for thin plastic.) If you want a high-vacuum system for forming thick plastic, the cost will be somewhat higher, depending mostly on how good a deal you find on a vacuum pump.
If you want to know how to make large, inexpensive vacuum formers, the troopers are the go-to guys.. With the book plans and a few tips from the discussion board, anybody can make a good large vacuum former. (Welding is not actually required; only common tools---a drill, a saw, etc.) Plenty of people there have also built smaller, even-less-expensive vacuum formers, including 12 x 18 inch setups that cost around $30 (using a kitchen oven and a vacuum cleaner), and taking only an hour or two to make; if you only want to build a small, very inexpensive vacuum former, you'll fit in fine. 2) The vacuum forming forum on the discussion board. Amateur and professional machinists hang out at CNCzone, and there are some professional plastics-forming people who post in the vacuum forming forum. 3) The vacuum forming forum.
(Hobbymolding is a site for primarily amateur molding and casting in a variety of materials.) One commercial site is also worthy of mention:. They sell Doug Walsh's classic book,, and his plans for the excellent Hobby-Vac and Proto Form machines. They also sell books and videos on molding and casting and other subjects, and sometimes surplus vacuum pumps. (You can get Thurston James's book there, too.). This is a blog associated with, a site for information on vacuum forming, moldmaking, and building vacuum formers. (Including our free vacuum former plans, as well as links to plans that cost money, from other sources.) I'll use this blog to post relevant information and get feedback, and link to the best stuff here from www.vacuumformerplans.com Actually, at this writing, the two sites are identical; the vacuumformerplans.com domain is hosted at vacuuumformerplans. (Eventually I intend to have a regular website at vacuumformerplans.com with standalone info, and selected links over here.) is meant to serve largely as an index to the best information available here and elsewhere, by us and by others.
Welcome to the Pepakura Vault I would like to thank every person who contributes to Pepakura and if you feel uncredited for anything on the site then please contact me and I will endeavor to rectify the problem ASAP. I can be contacted via the facebook page I run called the. In addition if you feel I am distributing your files without the proper consent then once again contact me and I will fix these issues too. Thanks again for looking. Cross Browser Support This site should be compatible with all major browsers. Compatible Browsers.
• • • • • • • • • • • • What is Pepakura? Pepakura is the art-form of building and creating with paper. The paper serves as a base for fiberglass, bondo (if you’re in USA or most body fillers for cars if you’re in UK), resin, and other 'hardeners'. The project is then sanded smooth and may also require some additional sculpting from modelling putty. After this the item can either be finalised or used as the start of a mold for either slush casting or for use in a vacuum former. The name of the original Pepakura Desginer software from TamaSoft. The software is required to create, view, and print your pepakura creations!
Get the FREE version of the software that allows you to view pep files and slightly alter them but if you are wishing to create your own from 3D models then you will need to purchase a full version licence. What can I create with Pepakura? Anything that you can create using a 3D programme means you can create a final 3D real version in real life with Pepakura.
Some classic pep project ideas include: Wearable Iron Man suits, War Machine, Halo props, Skyrim masks, realistic scale-model weapons, many different Star Wars props and when you learn the software, basically anything else you can think of! How do I get started? It's recommend heading over to TamaSoft to Download (click the image to download this software) the free version of their Pepakura software so that you can view and print Pepakura files. Next, do some searching around the internet or PepProsDataBase to find a project file you would like to create in.PDO file format. Print onto 110 lb cardstock.
(Available in the PepProShop.) If you have printer, you can print directly from the Pepakura software. If you do not have printer, you must convert to a.PDF to print without hassle either at work (just don’t get caught) or at many other locations that have printers. Get yourself some X-Acto knives, extra blades, and preferred glue. Super glue allows for fast working, but with little room for error, While Elmers-type glue provides room to fix mistakes with a little extra patience (I personally use UHU glue as this allows for numerous attempts at altering while sticking and dries relatively quick and hard) You may gather future supplies now, but note that the paper project itself will take some time to complete. For the future supplies I found google a life saver but it took a loooooooonnnng time to actually locate a good supplier. Site Editor: Shadowmultimedia Last Update: 2015 This is a Shadowmultimedia designed and operated site This web site is intended for educational purposes.
The pepakura files found here have not been created by myself although I have altered some of them slightly in regards to size and layout if the size did not suit me personally. In addition these files have been located via simple google searches and various facebook groups and can easily be found by anyone via google or one of the various prop making forums out there.